News - Jun 13, 2022 Cooking Organic Materials in the Cook Islands
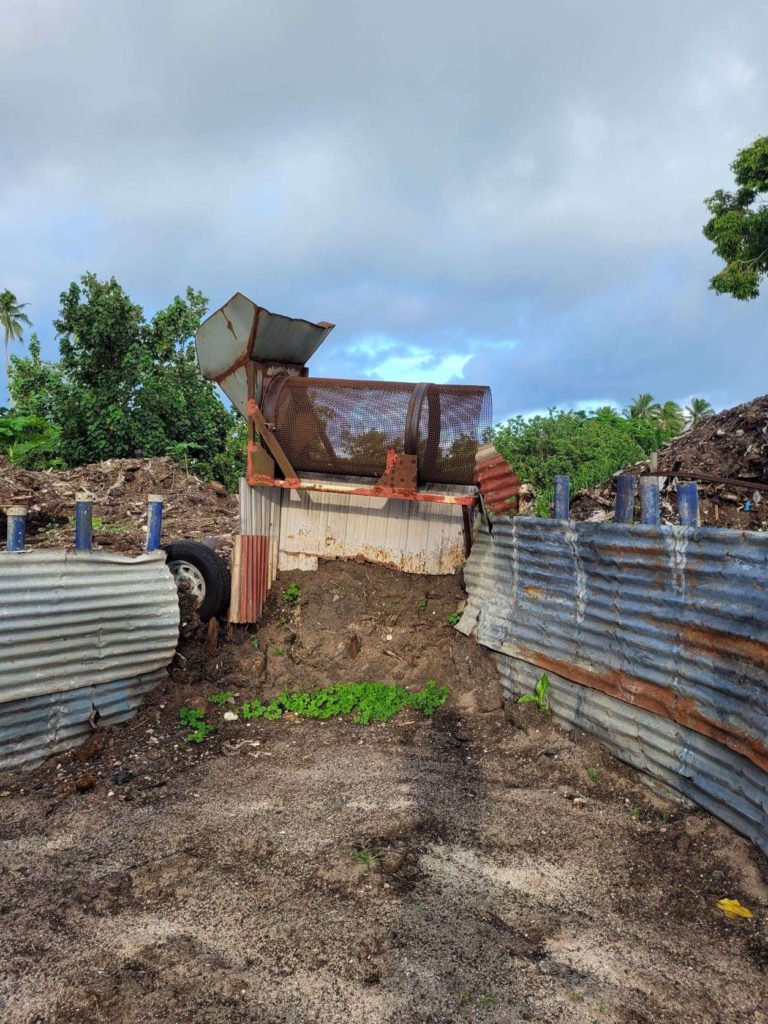
“There is no such thing as waste,” says Titikaveka Growers Association (TGA) founder and director, Teava Iro, “it’s only waste when we don’t know what to do with it.” This is the motivation for the establishment and ongoing operation of the TGA Compost Facility in Rarotonga, Cook Islands.
Iro, wanting to be part of sustainable and circular solutions to manage Rarotonga’s waste, receives approximately 15 tonnes of organic material per week and processes it into compost for sale back to the community. TGA started as an informal association of the growers living in and around Titikaveka village. The scheme slowly moved towards a business mode of operation, using donor aid from the New Zealand Development and Relief Agency to upscale the operation.
It is important to him to keep organic items from the landfill and turn them into something valuable. Landscaping material from hotels and by-products from the fish processing facility is the main material received at the TGA, processed at an 80|20 ratio. Other materials processed when available include by-products from noni agriculture and processing, coconut fronds, cardboard boxes, weeds, and pig manure.
These days Iro can manage the facility by “smell and feel” but in the beginning ran into problems. “The police turned up at 2 am in my first week,” Iro admits, “the whole neighbourhood couldn’t sleep because of the smell of rotting fish. I felt terrible!”.
But now there are no issues at all with odour.
A large pile open windrow composting method is used, and fish is added at an approximately 20% ratio, placed carefully inside the heap. The pile is kept aerated by regular turning and some large materials are kept in to also help with aeration and ensure it does not produce odour.
Trial and error over the years have also meant Iro now does not use a chipper to do any size-reduction on materials received. Some of the bigger logs and whole coconut are removed, but the rest of the material is simply placed on the pile, letting the good bacteria and micro-organisms do the work to break them down.
The main equipment used at the facility includes an eight-tonne excavator and a self-built sieve to screen the material prior to sale. Both are now undersized for the production throughput currently experienced.
Other than the need for larger equipment, the biggest challenge for Iro is managing the plastic being dropped off with organic material and other items like soil and even dumped vehicles over the weekend.
Opportunities for the future include finding a management solution for items received such as whole coconuts, such as experimenting with using the oil for biofuel and the husks for seedling trays and exploring making biochar to be used as a natural filtration.